Assembly Automation Case Studies: Robotic laser weld fabrication system
Explore the Assembly Automation Section
Automatic assembly machines and automation system solutions provide the best method for reducing labour costs, increasing output and eliminating manual handling concerns.
Explore this section to find out more about the how TQC can help you with your factory assembly automation processes
- Assembly Automation
- Pallet Transfer Systems
- Rotary Systems
- Assembly Benches
- Robotics and Handling
- Checking Jigs & Assembly Fixtures
- Case Studies
- Casting Multi-Position Screwdriving & Marking System
- Co-operating Robots
- Pallet Assembly System for Automotive Glovebox Latch
- Pallet Assembly System for Metal Pressed Parts
- Laser Marking & Verification System
- Lead Pot Robotic Handling System
- Automotive Plug Feed & Check System
- Poka Yoke Assembly Bench for Automotive Latch
- Bearing Automatic Heat, Press & Assembly System
- Hot Insert, Cold Insert & Seal Assembly/Check System
- Robotic Handling & Leak Test Cell
- Robotic Weld & Fabrication System
- SCARA Robot cell for Automatic Assembly of a Small Electrical Handset
- Semi-Automatic Assembly System for Automotive Radiators
- Cylinder Head Cover Clean, Assemble and Test Suite
- Automotive Hinge Assembly & Test System
Client: Global Engineering Company
Part: Engineering Metal Ring
Machine supplied: Robotic laser weld fabrication system
Overview: This system was designed and manufactured in order to give the customer the ability to automatically produce parts that were previously labour intensive within their production environment. TQC developed this system alongside the client to allow them to manufacture a range of parts in a quality assured manner at a high throughput.
Download details of this system as a PDF
Key features:
- Kawasaki 6-Axis Robot
- Reel fed material
- Multiple stations and sequential operations
- Laser welding and vision measurement and other technology modules incorporated
- PLC controlled
TQC have designed and manufactured a fully automatic manufacturing cell for the production of laser welded metal rings. The system incorporates multi stations that perform individual tasks to complete the manufacturing process, with a Kawasaki 6-axis robot being used to move product between the various manufacturing stations.
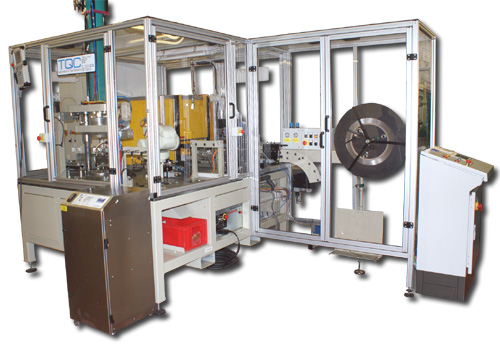
Robotic Weld Fabrication System
Reel fed material is measured out, cut to the correct length with the leading end presented for the robot to grip. The robot manipulates the strip to form the circular shape with a servo mounted gripper unit then securing the other end. The robot releases the part to allow it to be indexed into a fully guarded laser welding enclosure. The ends are welded together with vision inspection used to ensure the weld meets the required parameters.
Following welding, the ring is passed through a series of forming stations to complete the finished product. The final operation is to transfer completed parts to outfeed stack magazines. The control system monitors every station with part inspection included to ensure correct part production.
Throughout the system running, the robot manipulates parts between stations with any reject parts passed to a reject bin. The system manufactures several different sizes of rings.
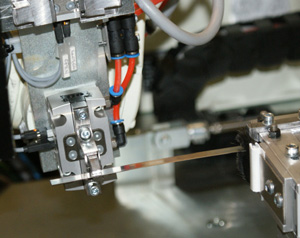
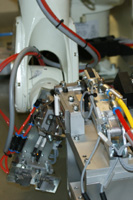
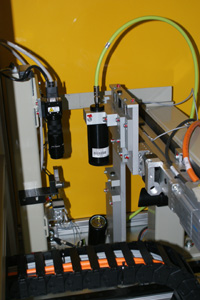
Details of the robotic laser weld fabrication system designed by TQC
To find out more about how we can help you with your automated or semi-automated assembly or robotic systems:
We build all machines in-house, applying our 25+ years experience in specialised test and automated handling machines to the engineering projects we undertake. We offer customer support, backup and service call-out for all projects, whatever the size.
Get in touch with us to discuss your requirements and we will be happy to offer our professional advice and visit you at your site.
- Contact us online
- Email us or call us on 0115 950 3561